Jak powstaje stal nierdzewna? Proces produkcji krok po kroku
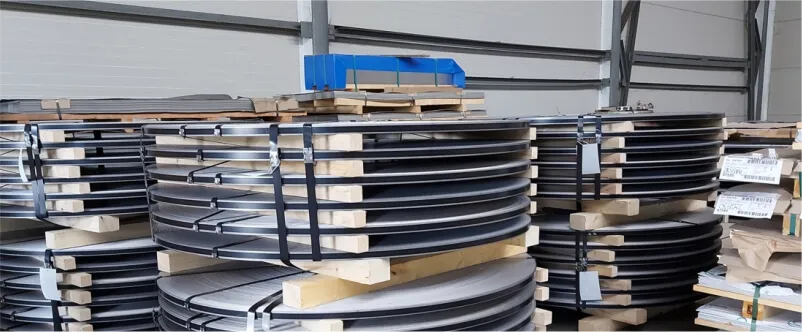
Stal nierdzewna jest jednym z najważniejszych materiałów wykorzystywanych w nowoczesnym przemyśle, technologii i budownictwie. Dzięki swoim unikalnym właściwościom, takim jak odporność na korozję, duża wytrzymałość oraz estetyczny wygląd, znajduje szerokie zastosowanie w wielu branżach. Proces jej produkcji jest skomplikowany i wymaga precyzyjnego doboru surowców oraz zaawansowanej technologii. Poniżej przedstawiono szczegółowy opis etapów, które składają się na produkcję stali nierdzewnej.
Czym jest stal nierdzewna i jakie ma właściwości?
Stal nierdzewna to rodzaj stali stopowej o zwiększonej odporności na korozję, którą zawdzięcza obecności chromu. Zazwyczaj zawiera co najmniej 10,5% tego pierwiastka, który tworzy na powierzchni metalu cienką, ale bardzo trwałą warstwę pasywną chroniącą przed działaniem tlenu i wilgoci. Dzięki temu można ją stosować w środowisku narażonym na czynniki atmosferyczne, wodę czy chemikalia.
Do najważniejszych cech jakościowej stali nierdzewnej zalicza się:
- Odporność na rdzewienie i działanie kwasów
- Wysoka twardość i trwałość mechaniczna
- Odporność na wysokie i niskie temperatury
- Łatwość obróbki oraz możliwość recyklingu
Właściwości te sprawiają, że stal nierdzewna jest niezwykle popularna w przemyśle spożywczym, budowlanym, chemicznym oraz medycznym. Dodatkowo, estetyczne wykończenie powierzchni umożliwia jej wykorzystanie także w projektach architektonicznych i designerskich.
Składniki surowe wykorzystywane w produkcji stali nierdzewnej
Podstawowym surowcem wykorzystywanym w produkcji stali nierdzewnej jest żelazo, do którego dodaje się odpowiednie proporcje innych pierwiastków stopowych. Najważniejszym z nich jest chrom , którego zawartość wpływa bezpośrednio na odporność na korozję. Pozostałe dodatki to nikiel , molibden , mangan oraz węgiel w śladowych ilościach ich proporcje zależą od konkretnego gatunku stali nierdzewnej i przeznaczenia końcowego produktu. Ważna jest jakość wykorzystywanych surowców i ich czystość chemiczna.
W celu otrzymania wysokogatunkowej stali stosuje się materiały pochodzące z wysokiej klasy hut. Warto rozważyć zakup stali nierdzewnej od sprawdzonego dostawcy, jak np. Rollsteel.pl, który oferuje szeroki wybór produktów wykonanych z wysokiej jakości stali nierdzewnej w tym blachy, pręty, kątowniki, rury i profile dostępne w różnych formach i gatunkach. To rozwiązanie idealne zarówno dla przemysłu, jak i dla indywidualnych inwestorów.
Topienie i oczyszczanie stopu pierwszy etap produkcji
Pierwszym konkretnym etapem produkcji stali nierdzewnej jest proces topienia surowców w piecach łukowych, w których temperatura może osiągać nawet 1700°C. W tym czasie zachodzą pierwsze reakcje chemiczne mające na celu wstępne ujednorodnienie i ewentualne usunięcie zanieczyszczeń. Dodanie odpowiednich proporcji pierwiastków i ich dokładne wymieszanie decydują o przyszłych właściwościach mechanicznych oraz odporności stali.
Po etapie topienia następuje proces rafinacji (oczyszczania), który eliminuje nadmiar siarki, fosforu oraz innych niepożądanych domieszek. Wykorzystuje się do tego m.in. technologie uzdatniania próżniowego, czyli degazacji, co poprawia czystość chemiczną stopu i jego właściwości techniczne.
Procesy walcowania, formowania i hartowania stali
Po oczyszczeniu i odlaniu stali do specjalnych form, następuje proces walcowania na gorąco. Materiał jest wstępnie formowany w postaci płyt, bloków, prętów lub taśm. W celu osiągnięcia bardziej konkretnego kształtu i wymiarów stosuje się walcowanie na zimno, które zapewnia wyższą precyzję i lepszą jakość powierzchni.
Następnie stal poddaje się procesom obróbki cieplnej, w tym hartowaniu i odpuszczaniu. Procesy te mają na celu poprawę struktury wewnętrznej stali, a także nadanie jej większej plastyczności i twardości w zależności od zastosowań. To etap, który istotnie wpływa na końcowe parametry mechaniczne materiału. Dzięki dokładnemu formowaniu oraz hartowaniu, stal nierdzewna może być bez problemu stosowana w wymagających warunkach od instalacji sanitarnych, po konstrukcje nośne i urządzenia przemysłowe.
Wykończenie powierzchni i kontrola jakości gotowego produktu
Ostatnim etapem produkcji jest wykończenie powierzchni. Można je przeprowadzać na wiele sposobów poprzez szlifowanie, polerowanie, trawienie chemiczne czy satynowanie. To nie tylko wpływa na wygląd, ale również na odporność korozyjną materiału. Powierzchnia gładka i pozbawiona mikroporażek minimalizuje ryzyko osadzania się zanieczyszczeń i tworzenia ognisk korozji.
Gotowy produkt przechodzi szereg testów jakościowych , które mają na celu sprawdzić, czy spełnia on odpowiednie normy techniczne oraz specyfikację klienta. Analizie podlegają takie parametry jak: skład chemiczny, struktura, odporność na rozciąganie, nasiąkliwość czy reakcja z czynnikami chemicznymi. Stal, która pomyślnie przejdzie przez wszystkie etapy kontroli, trafia następnie do sprzedaży lub dalszej obróbki specjalistycznej.
Autor: Artykuł sponsorowany